Research
Table of Contents
- IntroductionWhat are environmentally friendly smelting processes?
- Main Research Theme 1: Environmentally friendly tantalum (Ta) and niobium (Nb) smelting processes without hydrofluoric acid
- Main Research Theme 2: Promotion of resource recycling of byproducts generated during steel smelting (electrical pulse disintegration and magnetic separation)
- Main Research Theme 3: New ironmaking process using ammonium salts as a secondary raw material (de-carbonization and utilization of unutilized resources)
- Other Research Themes: Process to significantly reduce electric furnace dust (EAF dust)
- Other Research Themes: Ocean dumping of pumice (volcanic products from Fukutoku-Oka-no-Ba or Hunga Tonga-Hunga Ha'apai Volcano)
IntroductionWhat are environmentally friendly smelting processes?
Various metals are indispensable to daily life. Although large amounts of metals are smelted daily worldwide, the smelting process involves many challenges, including:
Our laboratory is working on a new "environmentally conscious smelting process" as an alternative to the conventional smelting process, focusing on the recycling of waste, utilization of low-grade and unused resources, and improvement in the efficiency of the manufacturing process.
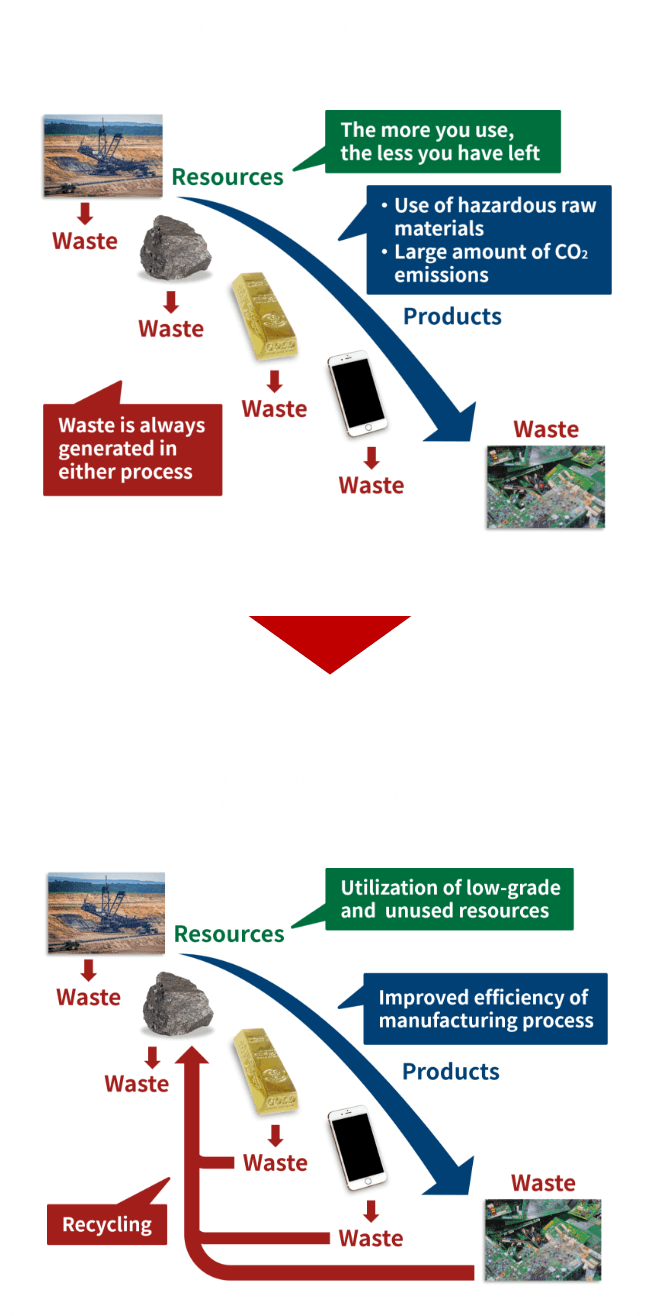
Main Research Theme 1Environmentally friendly tantalum (Ta) and niobium (Nb) smelting processes without hydrofluoric acid
Rare metals (minor metals), tantalum (Ta), and niobium (Nb) are widely used as raw materials for electronic materials and alloys, such as capacitors (Fig. 1-1). Since ores containing Ta and Nb are persistent, they are dissolved using hydrofluoric acid (HF) during the current smelting process (Fig. 1-2). However, HF is an extremely hazardous chemical that causes fatal accidents, and disposal of the sludge generated by liquid waste treatment is also troublesome. Recently, our laboratory has developed an innovative Ta and Nb smelting process that does not use HF.
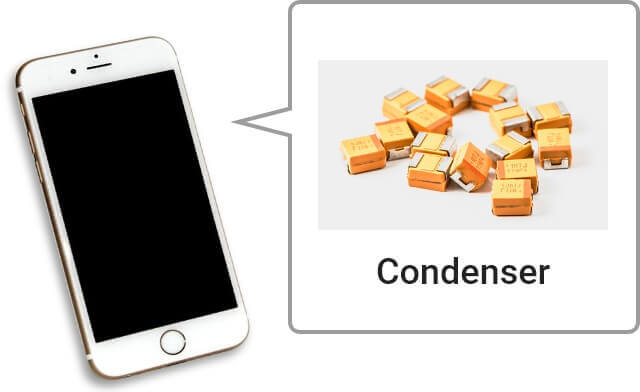
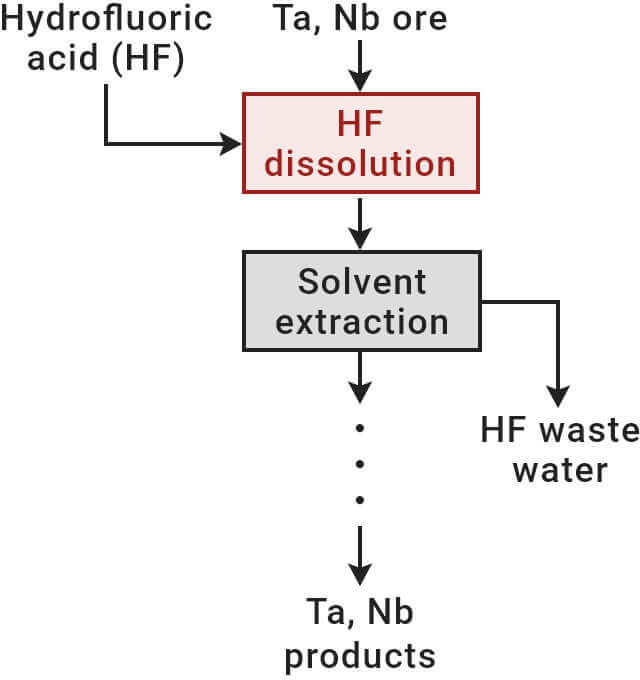
When solid ammonium hydrogen sulfate (NH4HSO4), Ta, and Nb ores are heated using a burner, a uniform molten salt is formed (Fig.1-3 ①-③). When the molten salt was allowed to cool and then leached with water, a white precipitate containing Ta and Nb formed (Fig.1-3 ④-⑤). This white precipitate was easily dissolved in acids other than hydrofluoric acid (sulfuric acid, hydrochloric acid, and nitric acid) (Fig. 1-3 ⑥). Furthermore, most of the Fe, Mn, and rare-earth elements, including Y, contained in the ore were dissolved in the filtrate.
Therefore, using this method, Ta and Nb ores can be dissolved in acid without the use of hydrofluoric acid and impurities can be easily removed. NH4HSO4 is cheaper than hydrofluoric acid and contains no strategic resources. This process has attracted attention as an innovative method for smelting Ta and Nb.
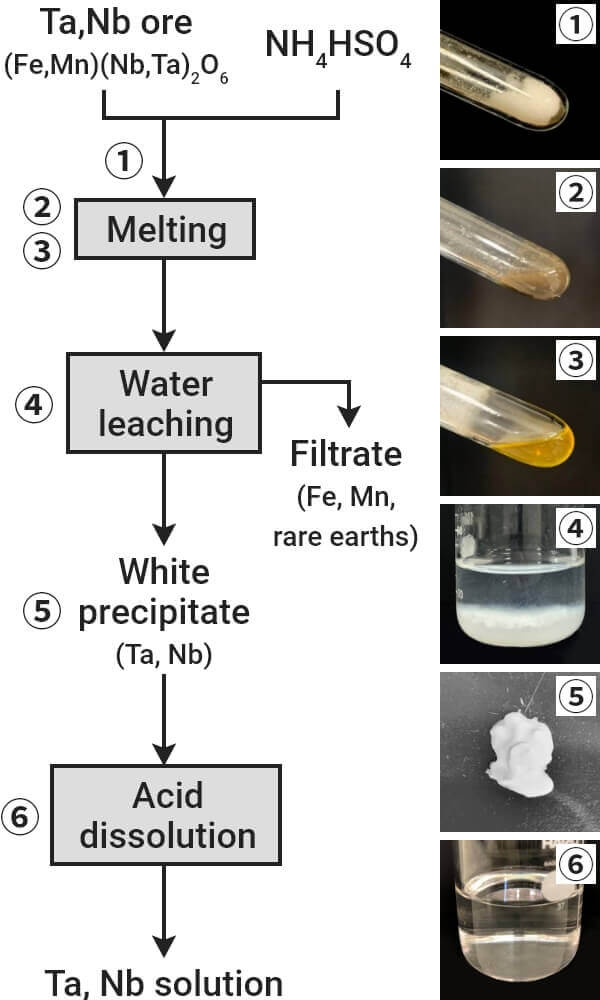
Related Patent
Title of invention | Registration date | Patent number | Link |
---|---|---|---|
Method for Liquefying Niobium and Tantalum and Method for Producing Niobium and Tantalum Solutions | July 9, 2021 | PCT No. WO 2022/196197 | View details |
Main Research Theme 2Promotion of resource recycling of byproducts generated during steel smelting (electrical pulse disintegration and magnetic separation)
In steel smelting, components other than iron derived from the raw materials are removed as slag. For example, steelmaking slag (Fig. 2-1 (a)) contains phosphorous (P) and manganese (Mn), which are strategic resources, and stainless-steel slag (Fig. 2-1 (c)) contains chromium (Cr), an environmentally controlled substance.
In addition, refractories attached to the points where they come into contact with molten iron and molten slag have to be replaced frequently. Hence, their effective use must be promoted. Spent refractories (Fig. 2-1 (b)) contain valuable materials such as aggregates, high-grade ceramics, and stainless-steel wires.
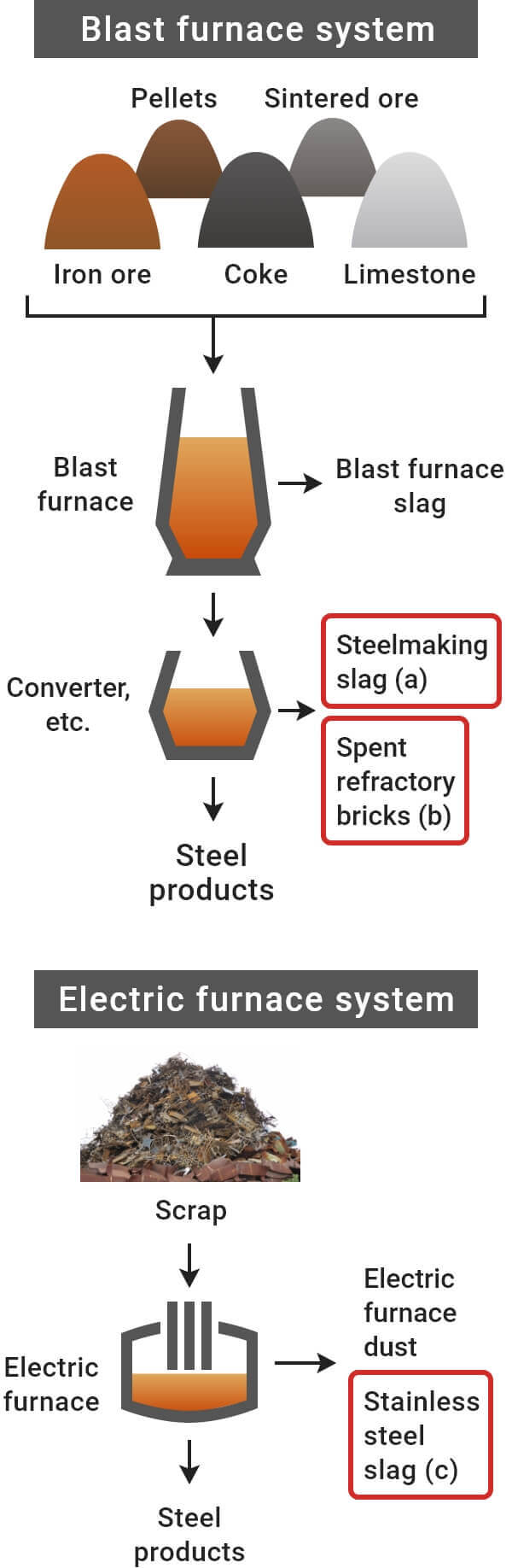
Since these target components form concentrated phases in the slag and refractories, they can be separated if they are pulverized cleanly to produce free particles. However, current milling methods mainly use impact and compressive forces, resulting in the generation of particles that are combined from multiple phases (single-blade particles) with low energy efficiency (Fig. 2-2 (a)).
We succeeded in selectively separating phases with concentrated target components using the electrical pulse disintegration method (Fig. 2-2 (b)), which can preferentially fracture at the boundaries of different phases, and the magnetic and specific gravity sorting methods (Fig. 2-3 (a)–(c)). Currently, we aim to realize a recycling process that comprehensively treats the slag and spent refractories generated during steel smelting (Fig. 2-4).
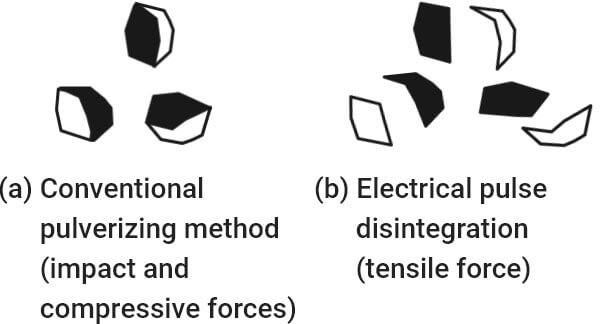
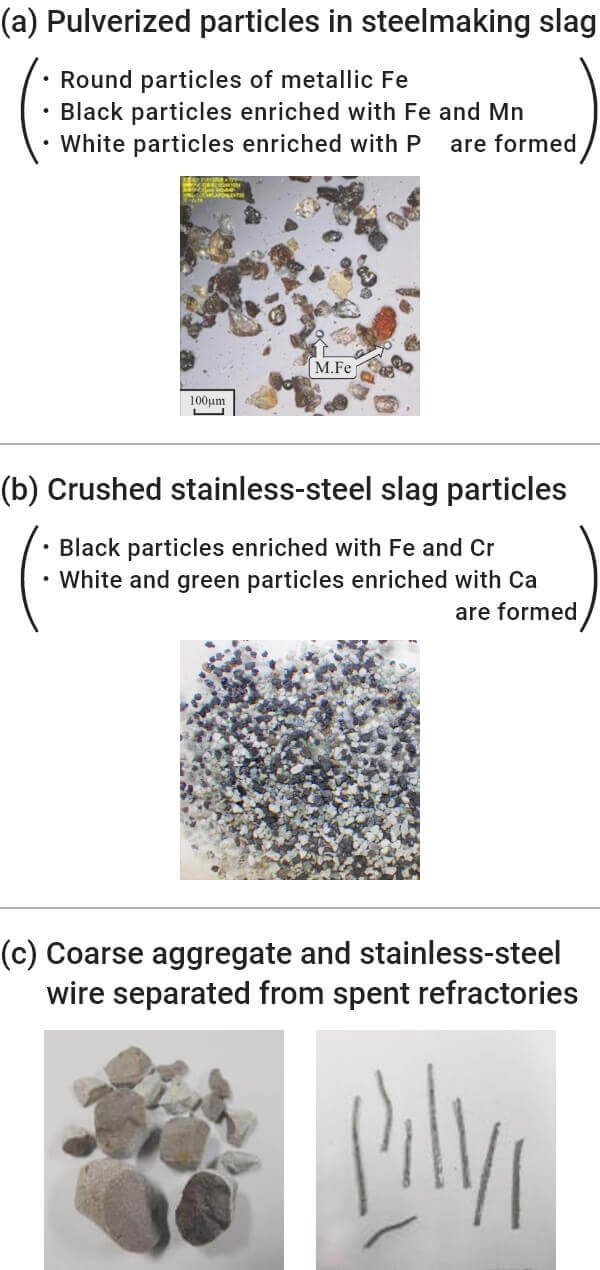
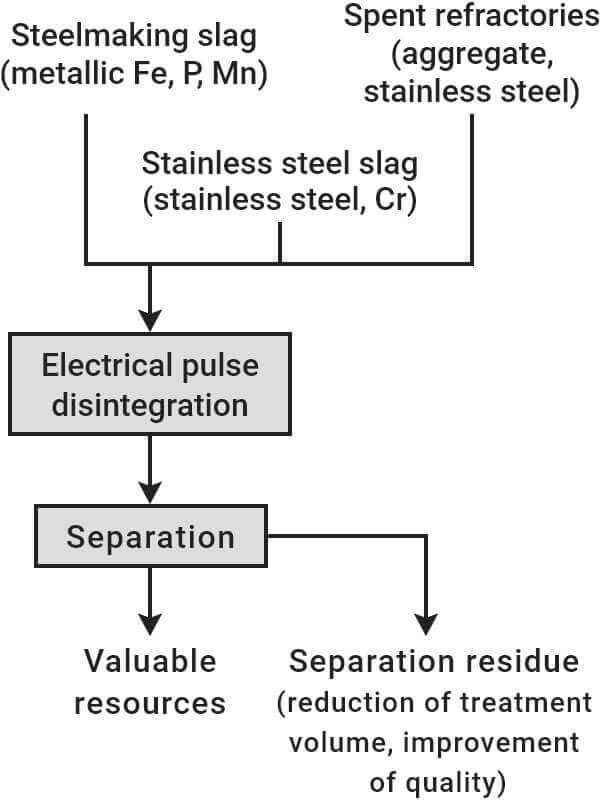
Related Patent
Title of invention | Registration date | Patent number | Link |
---|---|---|---|
Chromium Recovery Method | October 15, 2021 | 6961275 (in Japan) |
View details |
Related Paper
Title | Journal | Author | DOI |
---|---|---|---|
Removal of Phosphorus from High-phosphorus Iron Ore with Preliminary Reduction Treatment and Physical Concentration | ISIJ International 59(4) p.697-702 (2019) | Hironari KUBO, Nobuhiro MARUOKA, Yoshimasa SATO | View details |
Selective Separation of Metallic Fe Remaining in Slags Using Electrical Pulse Disintegration | ISIJ International 61(5) p.1725-1735 (2021) | Hironari KUBO, Masahiro NAKANISHI | View details |
Main Research Theme 3New ironmaking process using ammonium salts as a secondary raw material (de-carbonization and utilization of unutilized resources)
More than 10% of CO2 emissions in Japan are generated by the steel industry. New steelmaking methods using hydrogen, ammonia, and electricity instead of coal are being promoted as national projects, but the utilization of low-grade ores, resource recovery from slag, and reduction of limestone-derived CO2 remain unsolved (Fig. 3-1).
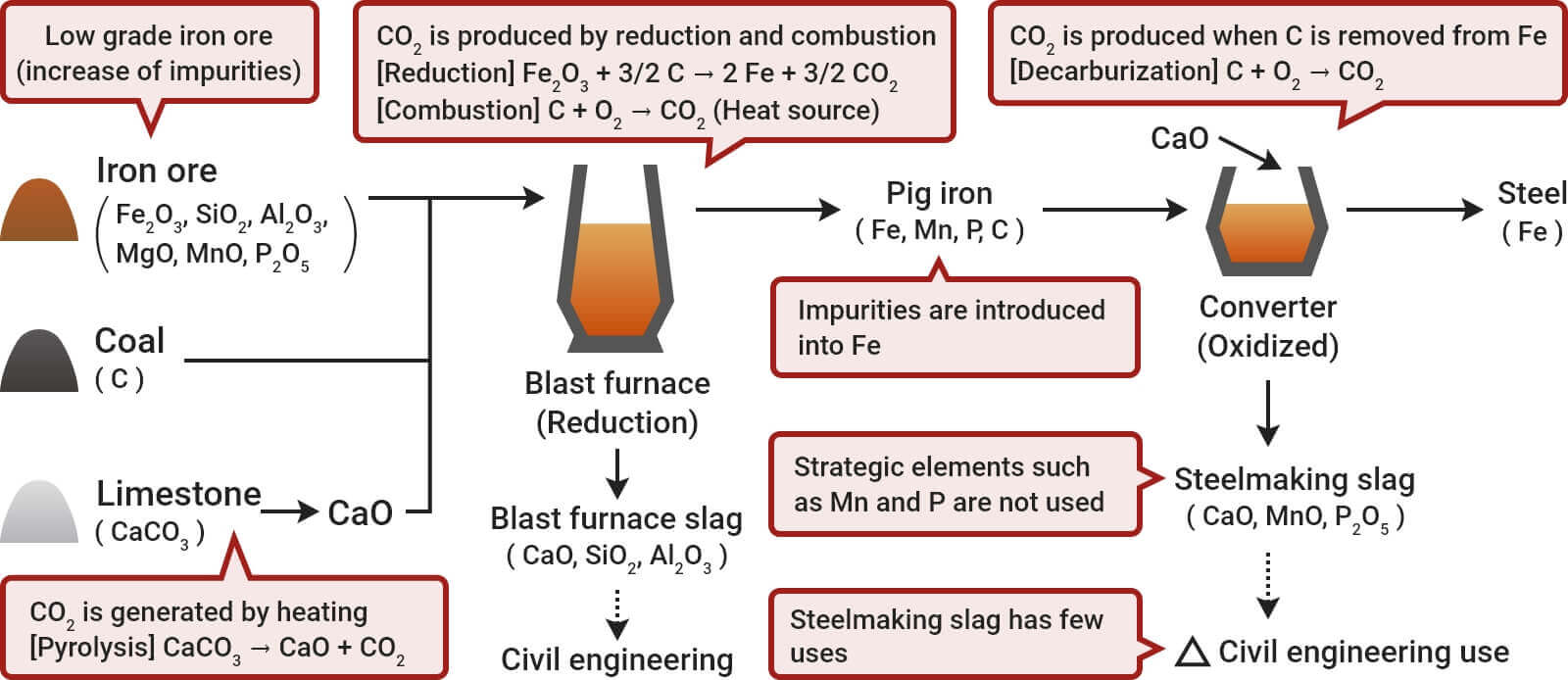
We have proposed an innovative "Ammonium salt ironmaking process" that can also solve these problems (Fig. 3-2). When iron ore reacts with ammonium chloride (NH4Cl) at approximately 500 ℃, Fe2O3 in the ore is converted into FeCl3, which has a lower boiling point, and volatile separation occurs without impurities. The reduction of this volatile matter yields high-purity iron that has never been attained before.
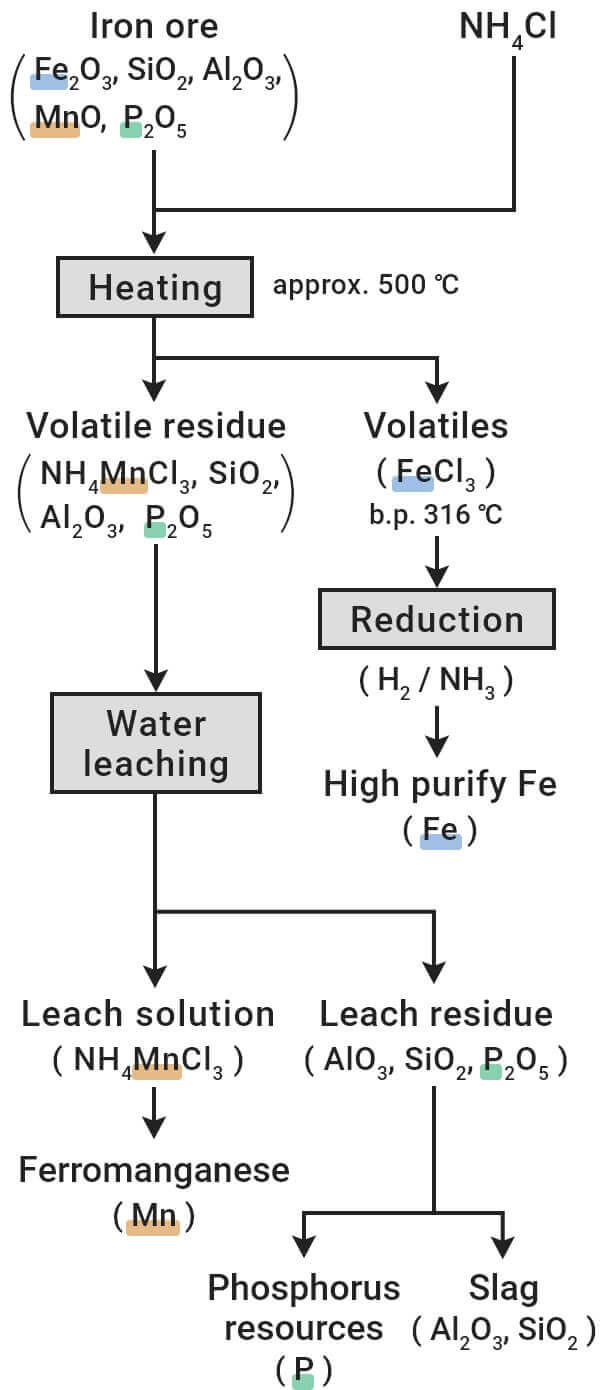
This process also has other advantages, which are as follows:
- (1) Low energy consumption because of no melting.
- (2) High-purity iron can be produced without being affected by low-grade iron ore.
- (3) No limestone was required, significantly reducing CO2and slag generation.
- (4) The Mn in iron ore can be utilized as a resource.
- (5) P can be easily utilized in other manufacturing processes.
- (6) NH4Cl is solid and can be transported and stored with ease.
Substituting other secondary raw materials (hydrogen, ammonia, electricity, and ammonium chloride) for the cheaper coal and limestone used in the current steel smelting process will inevitably lead to a significant increase in steel prices. In contrast, iron ore contains large amounts of strategic resources such as Mn and P, which are more expensive than Fe but are currently unutilized. Ammonium chloride ironmaking can utilize these strategic resources, thereby achieving a total cost advantage. Thus, we believe that the steel industry should be transformed from a business type that manufactures only iron to one that manufactures iron-ore-derived materials, including Mn and P, comprehensively.
Related Patent
Title of invention | Registration date | Patent number | Link |
---|---|---|---|
Treatment Method for Steelmaking Slag | October 18, 2021 | 6962536 (in Japan) |
View details |
Method for Steelmaking | December 3, 2021 | 6987419 (in Japan) |
View details |
Other Research ThemesProcess to significantly reduce electric furnace dust (EAF dust)
Electric furnace steelmaking, in which scrap is used as the main raw material to produce iron, generates fine particles with a diameter of approximately 1 µm, called EAF dust (Fig. 4-1). Although rich in Zn and Fe, EAF dust is a problematic waste that contains hazardous components such as Pb, Cd, F, and Cl.
Most of the EAF dust is separated into crude zinc oxide (sufficient quality for use in zinc smelting) and clinker (of poor use) using the carbon thermal reduction method as an intermediate treatment. However, this intermediate treatment method is inefficient, and the treatment cost is a heavy burden on electric furnace manufacturers.
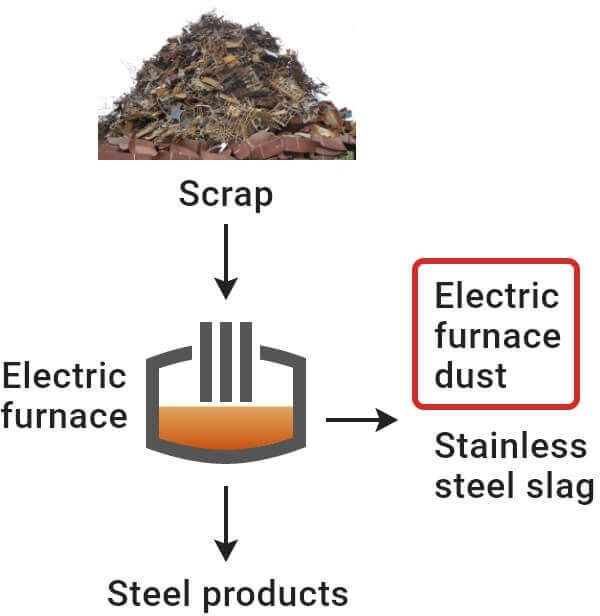
We have proposed a process that can significantly reduce the amount of EAF dust consigned to intermediate treatment by combining two popular technologies: magnetic separation and dust injection (Fig. 4-2).
First, the EAF dust is magnetically separated from the Zn-rich unmagnetized material to separate the Fe-rich magnetized material. When only the magnetized material with few impurities is dust-injected (re-blown into the electric furnace) into the next lot of molten steel, most of the Fe component is converted into slag and the rest into enriched dust. Although a detailed explanation is omitted because it requires specialized knowledge of electric furnaces, the amount of electric furnace dust to be consigned to intermediate treatment can be reduced by at least 20%. In addition, as shown in Fig. 4-2, various advantages can be obtained that significantly reduce the overall environmental impact.
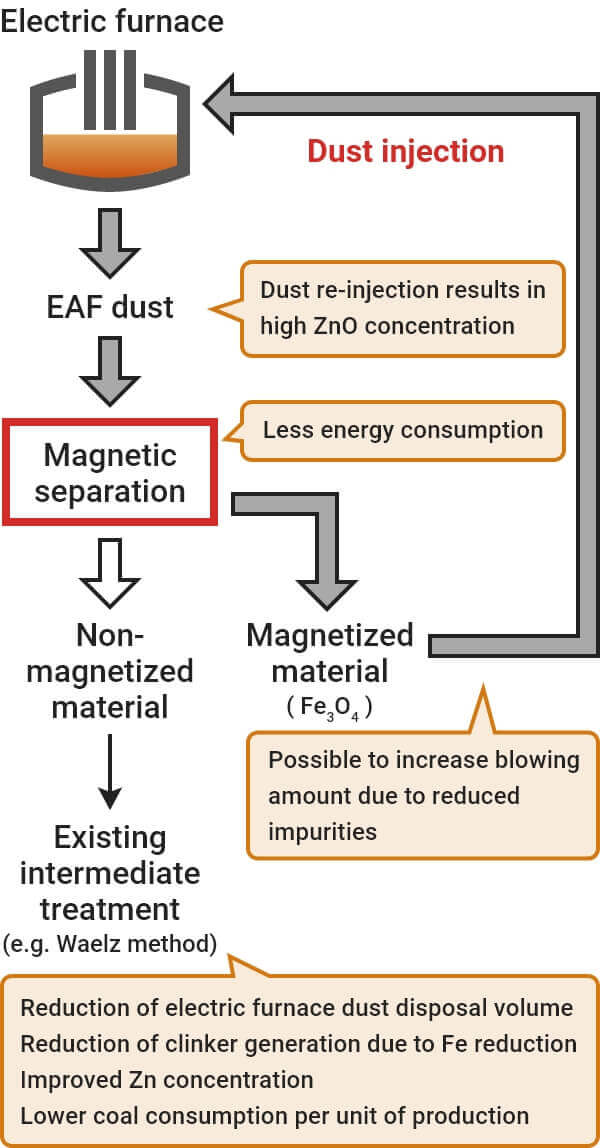
Related Patent
Title of invention | Registration date | Patent number | Link |
---|---|---|---|
Method of Treating Electric Furnace Dust | September 13, 2021 | 6943409 (in Japan) |
View details |
Other Research ThemesOcean dumping of pumice (volcanic products from Fukutoku-Oka-no-Ba or Hunga Tonga-Hunga Ha'apai Volcano)
A large amount of pumice ejected from an undersea volcano (Fukutoku Okanobo ) drifted ashore, mainly in Okinawa Prefecture, Japan, causing extensive damage to fishing and shipping activities in the region (Fig. 5-1). Although the recovery has significantly progressed, the disposal of a large amount of pumice stone remains a problem.
Although pumice does not contain any toxic components, it is impregnated with salts derived from seawater, limiting its use. Many applications have been proposed, including gardening materials, soil improvement materials, and blocks; however, the processing capacity and the supply-demand balance are unknown. Disaster waste is generated in large quantities at a time, and it is of utmost importance to complete treatment in a short time in a manner that has a minimal impact on society and the environment. Therefore, land disposal of pumice stones is not necessarily a rational measure.

Pumice contains few harmful components. The gas in the pumice reduces its apparent specific gravity, causing it to float. Even under natural conditions, pumice gradually becomes finer due to waves and particle collisions, and loses its floating nature as the amount of gas in it decreases. This is a natural continuous phenomenon; however, the process is believed to take at least several years. If pumice can be made to lose its floatability, it can be deposited on the seafloor as a harmless stone.
We succeeded in eliminating the floating nature of pumice by crushing and decompression treatment (Fig. 5-2). Both pulverization and depressurization are already perfected technologies, which can be easily scaled up and at low cost. Implementation of this technique at sea will enable most of the pumice to be spread thinly over a large area of ocean with minimal impact on the ecosystem. Ocean dumping of pumice is the most rational measure.
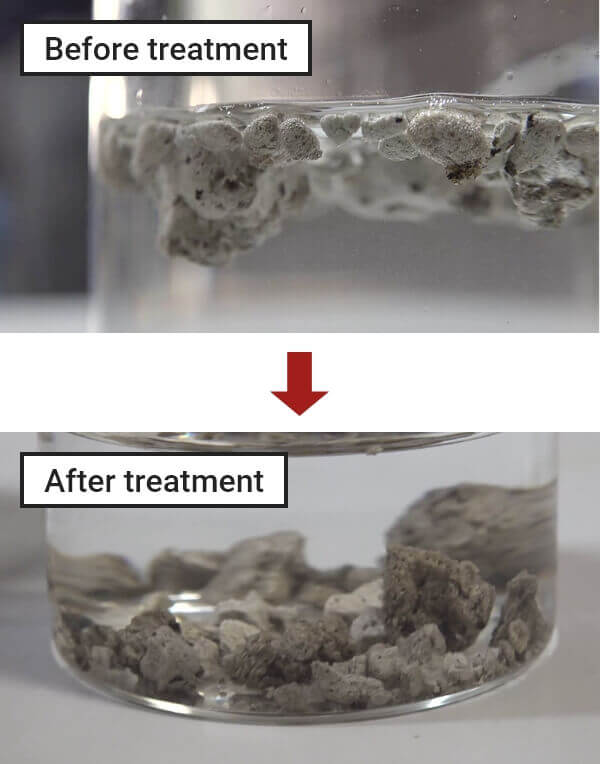
Related Patent
Title of invention | Filing date | Application number | Link |
---|---|---|---|
Method of Treating Pumice Stone and Dumping Pumice Stone | December 6, 2021 | JP-A2021-197541 (in Japan) |
ー |
- Home
- Research